Human-Robot Interaction
Despite recent advancements in robotics for autonomous operations in unstructured environments, their use in construction has been mostly limited to executing predefined plans. However, the unpredictable nature of construction sites and potential errors in planning necessitate higher adaptability in the execution setup to accommodate on-the-fly adjustments or reconfiguration of elements. Human-in-the loop fabrication workflows are particularly well-suited to address these challenges by blending the flexibility and intuition of humans with the precision of robots, creating a powerful partnership. For instance, this can enable humans to intervene in order to mitigate material uncertainties and positioning misalignments. Nevertheless, the interaction modalities between humans and machines typically require both actors to work in close proximity within hazardous environments posing safety risks and logistical difficulties. Moreover, the task of instructing the robots to make changes is challenging due to the scale of the structures being fabricated and the unintuitive robotic constraints.This workshop proposes a novel, hybrid synergetic workflow that enhances human-robot interaction (HRI) to support dynamic and reconfigurable fabrication processes. Humans can intervene by modifying a scaled-down version of the structure, thereby enabling more intuitive and safe adjustments in the building process.
In this workshop, participants will be introduced to collaborative robots (cobots) in the context of digital spatial assembly, their implementation challenges, and how human-in-the-loop strategies can help to overcome them. During the two days, they will get an overview of the digital tools and processes employed for hybrid human-robot construction teams and HRI strategies. We will work hands-on to collaboratively build a structure and explore how humans can intervene remotely in robotic assemblies by manipulating a work-in-progress small-scale physical model. The actions taken on the scaled physical model are recognized and processed with a custom computational tool that maps them to executable tasks for the collaborative robotic setup. This interaction method provides a hands-on medium for non-experts and establishes a communication protocol with the robotic setup outside of the construction zone. As such, our approach aims to lower the barrier for engagement with robotic construction processes and minimize safety risks when working in construction sites.
Initially, participants will interact with the small-scale model made of simplified props as a means of remote instruction and intervention within the robotic timber assembly process. They will be able to experiment and instruct remotely the placement of new elements, as well as disassembly and reconfiguration actions of the full-scale structure. Our system will capture human actions, enabling the creation of a digital counterpart for the small-scale model. A developed algorithm will provide feedback for the feasibility of the assembly or reconfiguration and instruct the human on the optimal sequence for adding or removing elements. The participant will make final adjustments based on this feedback and the robots will execute the required tasks.
The workshop will include interactive discussions and tutorials. Participants will also engage in hands-on experimentation and participate in the building of a demonstrator.
With this experimental setup, the workshop has the following objectives:
- Introducing how to operate ABB cobots (Gofas) and basic path planning within the COMPAS framework (compas_RRC and compas_fab packages)
- Exploring hybrid human-robot fabrication teams and task allocation strategies
- Experimenting with methods for human-robot interaction and communication protocols for reconfigurable structures
- Introducing methods for adaptive sequencing and temporary supports necessary for reconfigurable structures
- Hands-on application of the digital workflow: tracking changes in the scaled model and mapping them in the process-level digital model, translation to fabrication-feasible actions with the specific material system, generation of on-the-fly sequencing, needed supports, and motion planning, and finally execution of the planned actions with the collaborative hybrid team.
Required equipment: Laptop with Rhino 7 (or 8) installed (trial version is valid for 90 days). Other relevant libraries will be installed at the beginning of the workshop.
Workshop Leaders
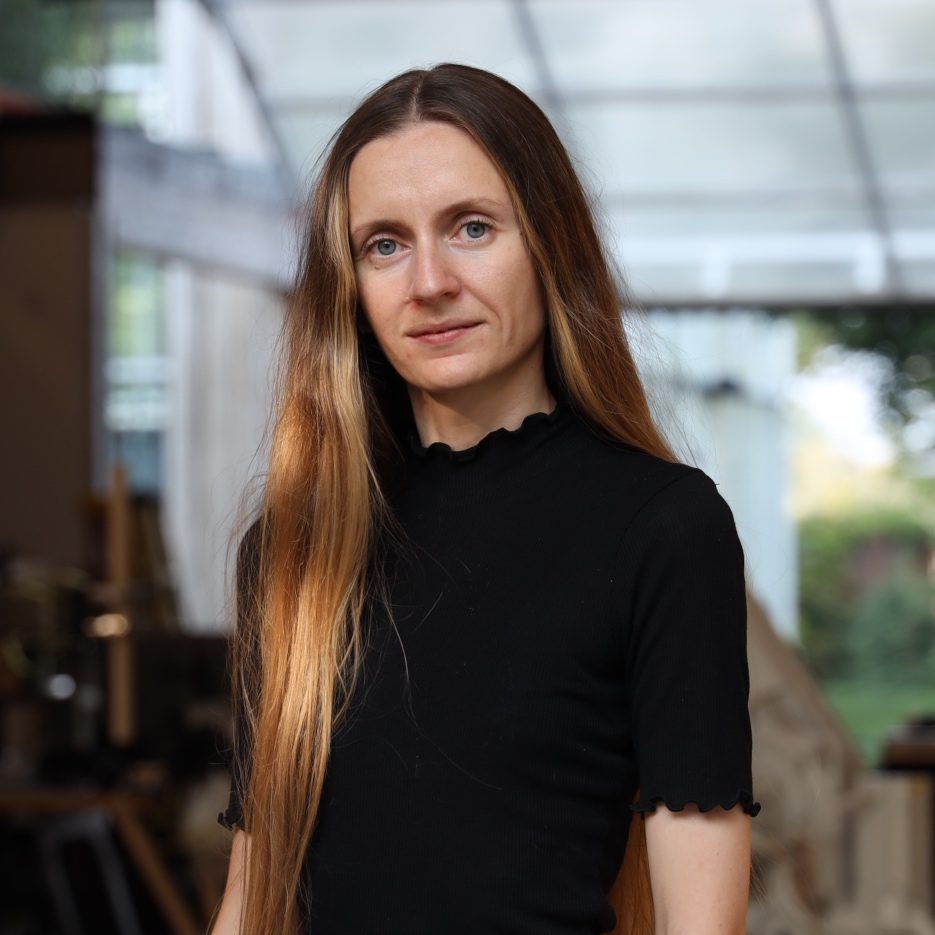
Stefana is researcher, architect, and educator whose work lies at the intersection of architecture, digital fabrication and computational design. She is currently an Assistant Professor at EPFL where she founded the Lab for Creative Computation. Through her research, she has explored multi-robotic fabrication methods and their relationship to architectural design. Stefana investigates computational design techniques ranging from agent-based systems to sequential design and optimisation methods. Her goal is to strengthen the connection between design, structure, and fabrication, and boost the interdisciplinary nature of architecture through the development of accessible computational tools and robotic fabrication methods. Before joining EPFL, Stefana was an Assistant Professor at Princeton University, where she led the CREATE Lab Princeton.
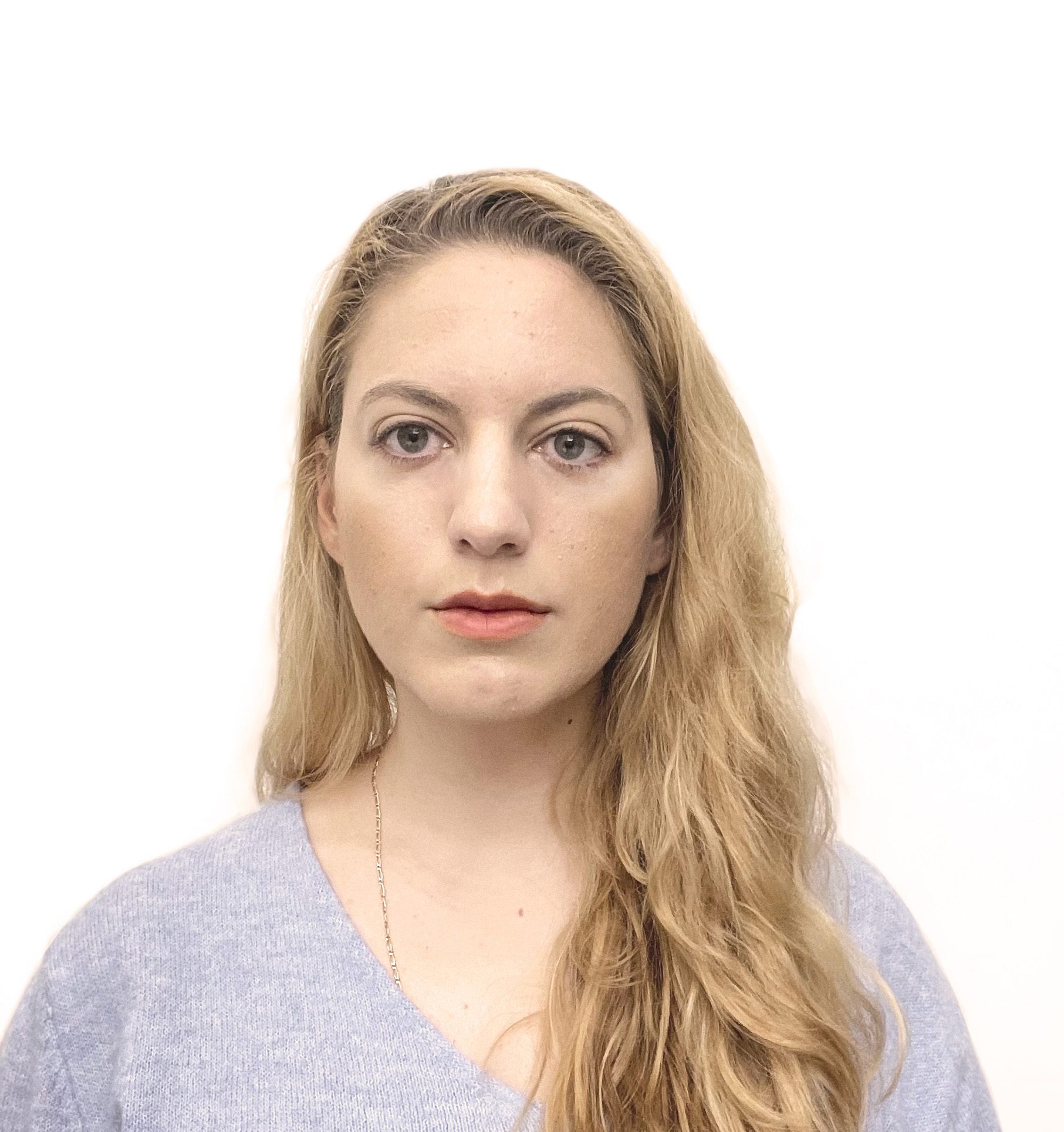
Eleni is a doctoral researcher at the Lab for Creative Computation (CRCL) at EPFL and associated to the National Centre for Competence in Research – Digital Fabrication. Before that, she was a research assistant at Digital Building Technologies, ETH Zurich working on additive manufacturing. She holds an integrated Master in Architectural Engineering from the National Technical University of Athens and an MAS in Architecture and Digital Fabrication from ETH Zurich. Her research explores human-robot interaction within heterogeneous construction teams. Eleni has taught various courses at ETH Zurich and EPFL at the undergraduate and graduate level.
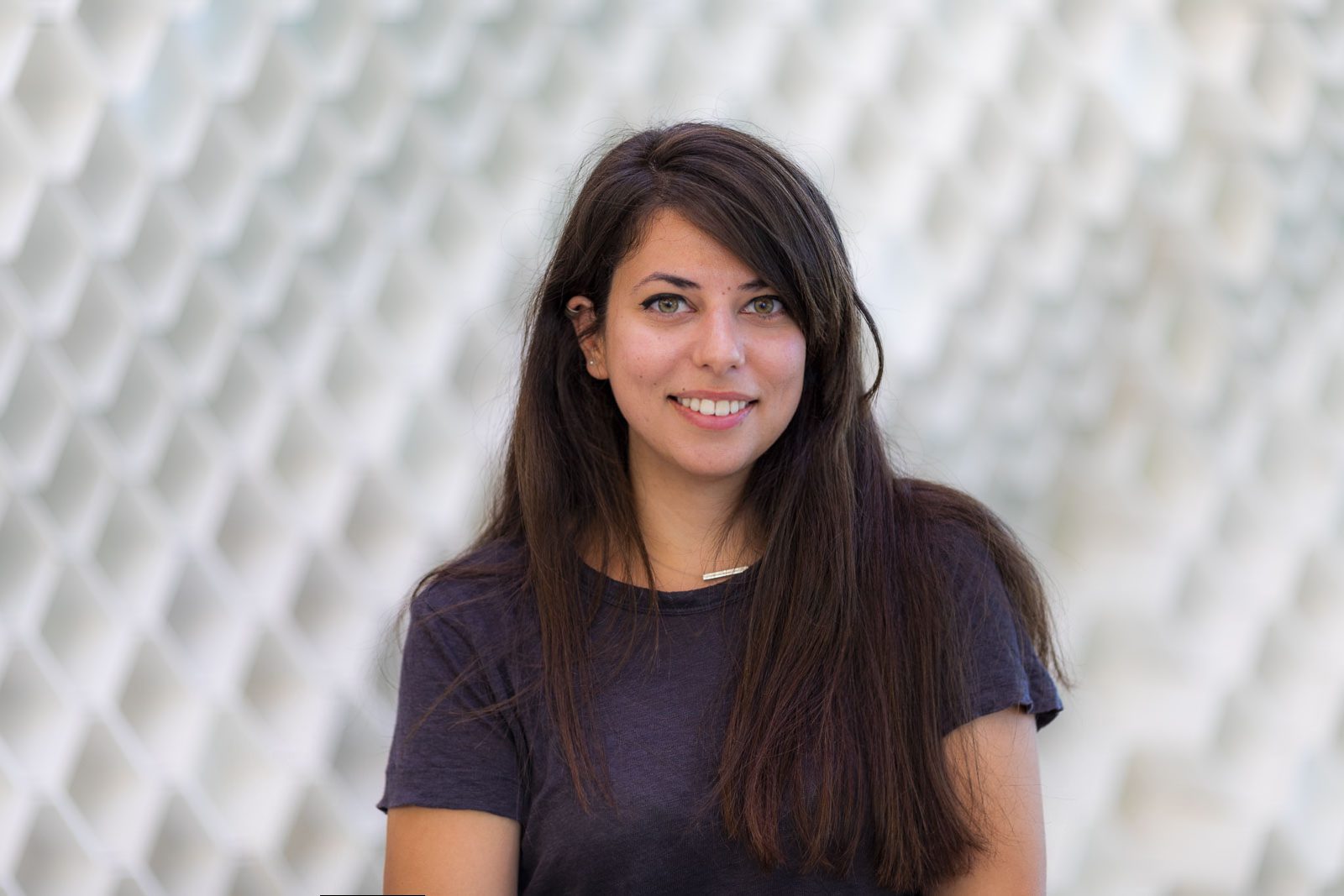
Marirena is a postdoctoral researcher jointly appointed at the Creative Computation Lab and the Structural Xploration Lab at EPFL where she investigates human-robot collaborative workflows for structural reconfiguration and reuse of damaged timber structures. She gained her PhD from ETH Zurich in 2023 where she developed a digital framework for bespoke structures with 3D printed connections as an NCCR Digital Fabrication doctoral fellow. She holds a Diploma in Architectural Engineering from NTUA and an MAS in Digital Fabrication from ETH Zurich. Before her doctoral studies she was a visiting researcher at the Transformable Intelligent Environments Laboratory of TUC. Marirena brings a wealth of educational experience leading design studios and supervising students at the ETH Zurich, EPFL, and HSLU Luzern.
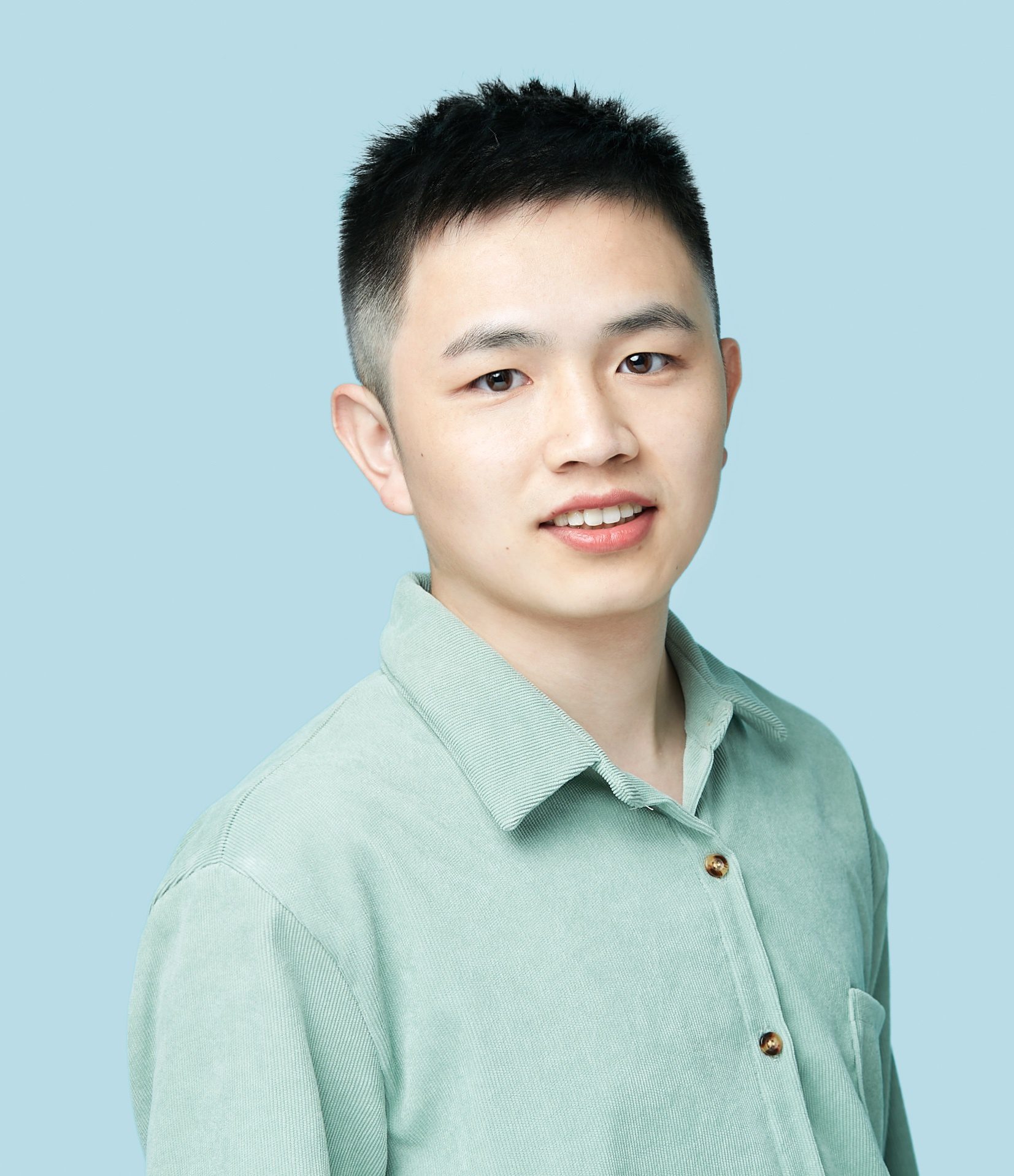
Ziqi is a postdoctoral researcher jointly appointed at the Creative Computation Lab and Sycamore at EPFL. Prior he was a postdoctoral researcher at the Computational Robotics Lab, ETH Zurich, advised by Prof. Stelian Coros. He obtained his Ph.D. at the School of Computer and Communication Sciences at EPFL. He received his bachelor’s degree in Mathematics in 2017 from University of Science and Technology of China. His research interests focus on geometry processing, architecture geometry, and digital fabrication. Ziqi has extensive teaching experience at both ETH Zurich and EPFL.